当废气具有大风量低质量浓度的特性时,可利用沸石转轮内部分子筛低温高吸附与高温高脱附的特点,对废气进行吸附-脱附浓缩。所产生废气的质量浓度约为原气体质量浓度的10~20倍,为后续催化氧化处理节约了设备与运营成本。
When the exhaust gas has the characteristics of high air volume and low mass concentration, the characteristics of low-temperature high adsorption and high-temperature high desorption of the molecular sieve inside the zeolite wheel can be utilized to adsorb and desorb the exhaust gas. The mass concentration of the generated exhaust gas is about 10-20 times that of the original gas, saving equipment and operating costs for subsequent catalytic oxidation treatment.
沸石浓缩转轮结构分为吸附区(A区)、在生区(R区)与冷却区(P区)。由加工好的波纹形以及平板状陶瓷纤维纸采用无机黏合的方式制成蜂窝状转轮,再将具有疏水性的沸石分子筛涂抹在转轮通道上,使其具有吸附性。沸石分子筛的化学通式为Mx/m[(AlO2)x·(SiO2)y]·zH2O,是一种结晶硅酸铝金属盐的多孔晶体,其中的硅氧四面体和铝氧四面体通过共享氧原子相互连接形成骨架结构。分子筛晶体的内部具有不同大小的孔穴,可以吸附比自身孔径小的分子,排出比其孔径大的分子。包装印刷行业废气的相对湿度一般小于70%,沸石转轮对VOCs的吸附率可达到90%以上。随着废气相对湿度的增加,吸附效率会有所下降,因此,可在废气进入沸石转轮前对其进行加热。根据风量,设置沸石转轮以1~6r/h的速率进行旋转。
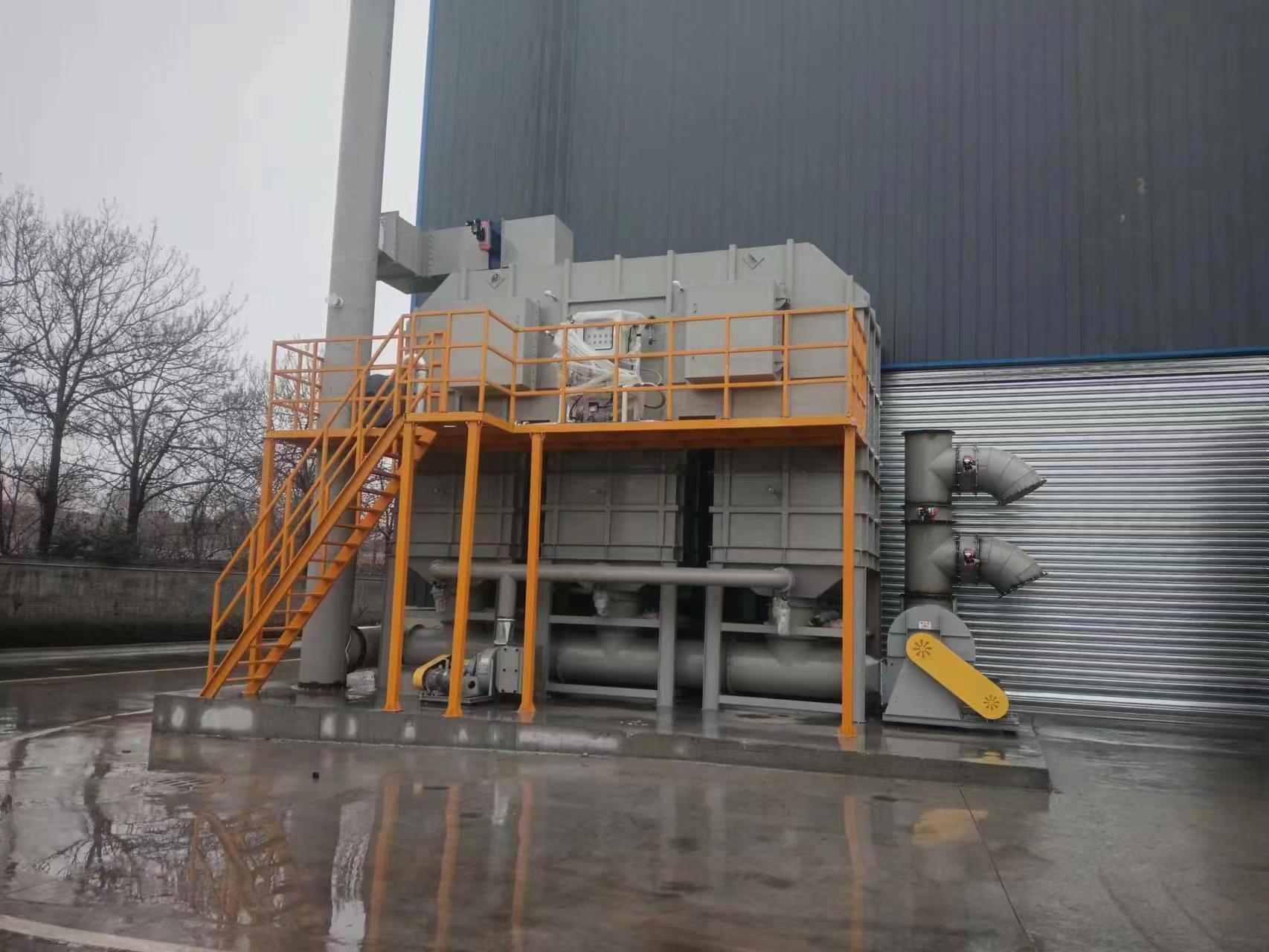
The structure of the zeolite concentration wheel is divided into adsorption zone (A zone), living zone (R zone), and cooling zone (P zone). The honeycomb shaped runner is made of processed corrugated and flat ceramic fiber paper by inorganic bonding, and then hydrophobic zeolite molecular sieves are applied to the runner channel to make it adsorbable. The chemical formula of zeolite molecular sieve is Mx/m [(AlO2) x · (SiO2) y] · zH2O, which is a porous crystal of crystalline aluminum silicate metal salt. The silica tetrahedra and alumina tetrahedra are interconnected by shared oxygen atoms to form a skeleton structure. The internal pores of molecular sieve crystals have different sizes, which can adsorb molecules with smaller pore sizes and expel molecules with larger pore sizes. The relative humidity of exhaust gas in the packaging and printing industry is generally less than 70%, and the adsorption rate of VOCs on zeolite wheels can reach over 90%. As the relative humidity of the exhaust gas increases, the adsorption efficiency will decrease. Therefore, the exhaust gas can be heated before entering the zeolite runner. According to the air volume, set the zeolite wheel to rotate at a rate of 1-6r/h.
沸石转轮用分子筛材质不可燃、an全性好,可在高温下进行脱附在生,其使用寿命长达5~10年。催化氧化工段所采用的氧化催化剂VOCs处理效率大95-98,对于间歇性工况废气,催化氧化比蓄热式催化燃烧法节能。氧化反应采用的催化剂使用寿命长,平均5年更换一次,并可作在生处理。整体装置采用低温燃烧,既节约能源又具有高的an全性。
The molecular sieve material used for the zeolite runner is non combustible and has good integrity. It can be desorbed at high temperatures and has a service life of up to 5-10 years. The VOCs treatment efficiency of the oxidation catalyst used in the catalytic oxidation section is 95-98% higher. For intermittent exhaust gas conditions, catalytic oxidation is more energy-saving than regenerative catalytic combustion method. The catalyst used in the oxidation reaction has a long service life, with an average replacement time of 5 years and can be used for in life treatment. The overall device adopts low-temperature combustion, which not only saves energy but also has high integrity.
VOCs沸石转轮-催化氧化装置采用沸石浓缩与催化剂氧化组合技术,由多级过滤器、沸石转轮、吸附风机、脱附风机、换热器、催化氧化装置等分段设备组成,含有VOCs 的废气先经过初步多级过滤后,由鼓风机送至沸石转轮分段装置吸附区(A 区)进行吸附处理,生成的洁净空气被直接排出。随着沸石转轮的不停旋转,已饱和的转轮吸附区部分转至在生区(R 区),接受来自反向高温在生空气的吹洗并进行脱附。脱附后的浓度废气直接进入催化氧化装置进行氧化分解。经过脱附区的VOCs废气随后旋转进入冷却区(P 区),降温后返回吸附区进行循环操作。由于脱附在生区的空气风量一般仅为处理区风量的1/10, 因此在生后废气中的VOCs质量浓度约为浓缩前的10 倍。
The VOCs zeolite runner catalytic oxidation device adopts a combination technology of zeolite concentration and catalyst oxidation, consisting of multi-stage filters, zeolite runners, adsorption fans, desorption fans, heat exchangers, catalytic oxidation devices, and other segmented equipment. The waste gas containing VOCs is first subjected to preliminary multi-stage filtration, and then sent by a blower to the adsorption area (Zone A) of the zeolite runner segmented device for adsorption treatment. The generated clean air is directly discharged. With the continuous rotation of the zeolite wheel, the saturated adsorption zone of the wheel partially shifts to the living zone (R zone), receiving blowing and desorption from reverse high-temperature living air. The desorbed concentration of waste gas directly enters the catalytic oxidation device for oxidative decomposition. The VOCs exhaust gas passing through the desorption zone then rotates into the cooling zone (P zone), and after cooling, returns to the adsorption zone for circulation operation. Due to the fact that the air volume desorbed in the raw area is generally only 1/10 of the air volume in the treatment area, the mass concentration of VOCs in the waste gas after production is about 10 times that before concentration.
沸石转轮在生浓缩后的浓度废气被吹入下游催化氧化装置,并由燃烧器对其进行升温,预热至350℃后进行催化氧化反应。催化氧化全过程采用蜂窝状铂(Pt)触煤,废气中VOCs 经催化氧化反应生成二氧化碳与水。
The concentrated waste gas from the zeolite runner is blown into the downstream catalytic oxidation device and heated by the burner. After preheating to 350 ℃, the catalytic oxidation reaction is carried out. The entire process of catalytic oxidation uses honeycomb like platinum (Pt) to contact coal, and VOCs in the exhaust gas undergo catalytic oxidation reaction to generate carbon dioxide and water.
通过催化氧化工段后,被排出的净化气体温度约为360 ℃;为充分利用余热,将催化氧化设备净化后的气体与在生用废气进行热交换,升温后的在生废气用于沸石转轮脱附区的脱附。
After passing through the catalytic oxidation section, the temperature of the purified gas discharged is about 360 ℃; In order to fully utilize the waste heat, the purified gas from the catalytic oxidation equipment is heat exchanged with the live exhaust gas, and the heated live exhaust gas is used for the desorption of the zeolite runner desorption zone.