沸石转轮废气处理系统主要由两部分组成:废气浓缩系统和废气焚烧处理系统。
The zeolite runner exhaust gas treatment system mainly consists of two parts: exhaust gas concentration system and exhaust gas incineration treatment system.
废气浓缩主要通过沸石转轮实现,转轮为圆形结构,内部均匀填充沸石,而沸石的主要成分是多孔的骨架型硅铝酸盐,其内部分布着孔穴,具有对大小不一的分子进行选择性吸附的特性,故沸石转轮也被称为分子筛。沸石转轮在不同温度下具有不同的吸附效率,故安装转轮的风箱根据转轮的特性设置了3个分区:吸附区、脱附区、冷却区。
The concentration of waste gas is mainly achieved through zeolite wheels, which have a circular structure and are uniformly filled with zeolite. The main component of zeolite is a porous framework type aluminosilicate, with pores distributed inside, which have the characteristic of selective adsorption of molecules of different sizes. Therefore, zeolite wheels are also known as molecular sieves. The zeolite wheel has different adsorption efficiency at different temperatures, so the wind box installed with the wheel is divided into three zones based on the characteristics of the wheel: adsorption zone, desorption zone, and cooling zone.
涂装车间产生的废气通过汇总风道汇总后,经风管传输到转轮风箱进风口,废气在进入沸石转轮之前,设置3道过滤器,用于将废气中含有的杂质、颗粒去除,防止将沸石转轮堵塞。
The exhaust gas generated in the painting workshop is collected through a collection duct and then transmitted to the inlet of the runner wind box through the duct. Before the exhaust gas enters the zeolite runner, three filters are installed to remove impurities and particles contained in the exhaust gas and prevent blockage of the zeolite runner.
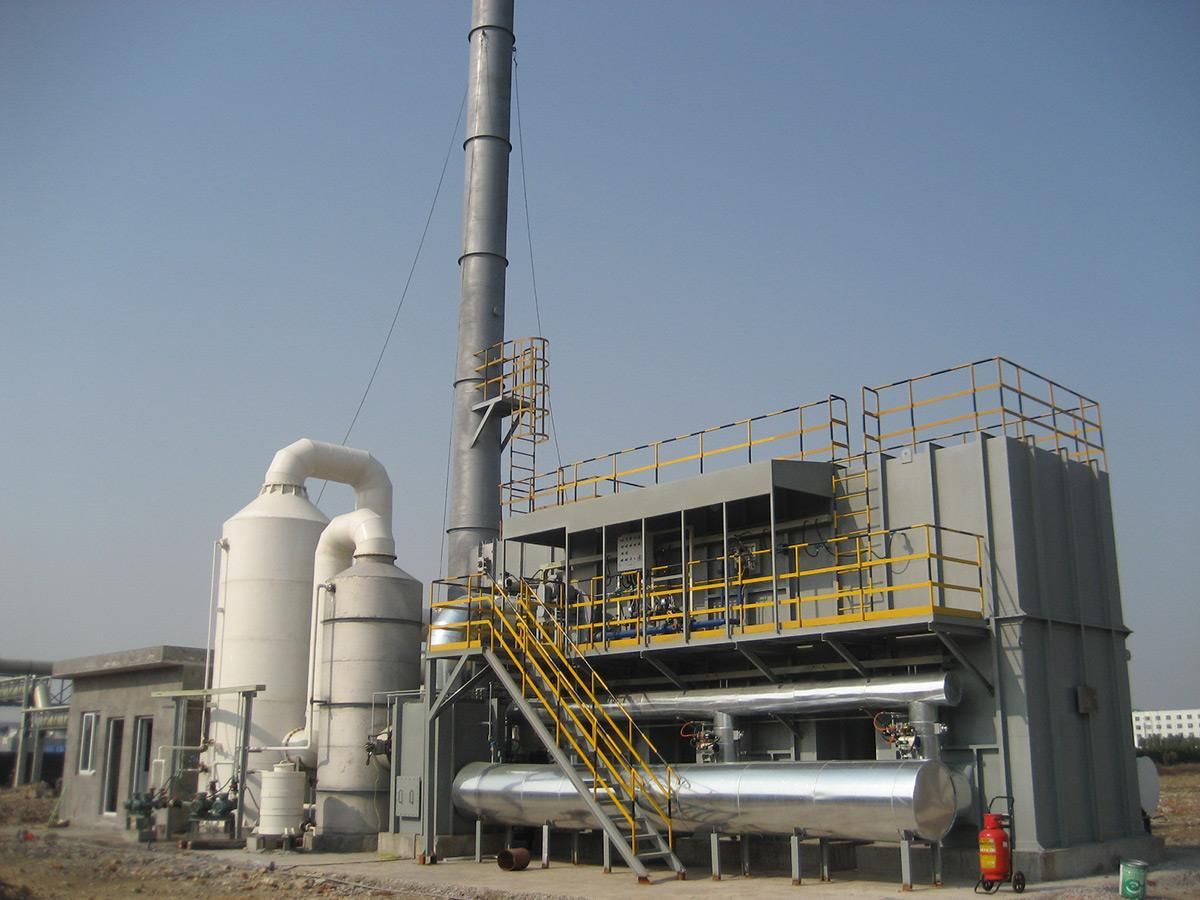
车间废气经过调温调湿及过滤后,进入转轮风箱的吸附区,大部分废气成分被转轮吸附,少量废气成分随着净化后的废气被直接排放,转轮在吸附的过程中不停地转动,吸附区吸收了大量废气成分后转动至脱附区,此时来自RTO的高温烟气通过与部分的车间废气混合达到250℃后通向脱附区,因为沸石转轮在250℃高温的情况下吸附效率较低,在吸附区吸附的废气成分在脱附区会重新被脱附下来,随着高温烟气被输送至RTO里进行废气焚烧处理,焚烧产生的烟气一部分用于转轮入口废气的升温除湿,另一部分送至脱附区进行脱附。
After temperature, humidity, and filtration, the workshop exhaust gas enters the adsorption area of the rotary fan. Most of the exhaust gas components are adsorbed by the rotary fan, and a small amount of exhaust gas components are directly discharged with the purified exhaust gas. The rotary fan continuously rotates during the adsorption process. The adsorption area absorbs a large amount of exhaust gas components and then rotates to the desorption area. At this time, high-temperature flue gas from RTO is mixed with some workshop exhaust gas to reach 250 ℃ before leading to the desorption area, Due to the low adsorption efficiency of the zeolite wheel at a high temperature of 250 ℃, the waste gas components adsorbed in the adsorption zone will be re desorbed in the desorption zone. As the high-temperature flue gas is transported to the RTO for waste gas incineration treatment, some of the flue gas generated from incineration is used for heating and dehumidification of the exhaust gas at the inlet of the wheel, and the other part is sent to the desorption zone for desorption.
旋转RTO由上至下可以分为3个部分:分风室、蓄热室、燃烧室。蓄热室里均匀分布着蜂窝状陶瓷蓄热体,在加热期流过格孔的高温烟气将热量传递给蜂窝陶瓷蓄热体,在冷却期,低温的废气以相反的方向流过格孔并获得热量,形成高温废气,所以陶瓷蓄热体的通过性直接影响着废气处理效率及RTO设备运行能耗。
The rotating RTO can be divided into three parts from top to bottom: air distribution chamber, heat storage chamber, and combustion chamber. The honeycomb shaped ceramic heat storage body is evenly distributed in the heat storage chamber. During the heating period, the high-temperature flue gas flowing through the grid holes transfers heat to the honeycomb ceramic heat storage body. During the cooling period, the low-temperature exhaust gas flows in the opposite direction through the grid holes and obtains heat, forming high-temperature exhaust gas. Therefore, the trafficability of the ceramic heat storage body directly affects the efficiency of waste gas treatment and the energy consumption of RTO equipment operation.
故旋转RTO在设计时考虑了蓄热陶瓷体的吹扫功能。初的设计为在RTO旁边设置吹扫风机,直接采用室外新风对蓄热陶瓷进行吹扫,但设备运行时发现:
Therefore, the design of the rotating RTO takes into account the blowing function of the thermal storage ceramic body. The initial design was to install a blowing fan next to the RTO, directly using outdoor fresh air to blow the thermal storage ceramic. However, during equipment operation, it was found that:
1)因为室外新风温度较低,吹入的冷风导致蓄热陶瓷及燃烧室温度降低,所以,设备运行时天然气耗量较大,增加了能源成本;2)设备运行时,RTO进气量与排气量均衡,当吹扫风机补入部分风量时,破坏RTO内部风平衡,且容易造成燃烧室内部压力增大。
1) Due to the low temperature of outdoor fresh air, the cold air blown in leads to a decrease in the temperature of the thermal storage ceramic and combustion chamber, resulting in a higher natural gas consumption during equipment operation and an increase in energy costs; 2) When the equipment is running, the intake and exhaust of RTO are balanced. When the blowing fan replenishes a portion of the air volume, it can disrupt the internal air balance of RTO and easily increase the pressure inside the combustion chamber.
故设备厂家对吹扫功能进行优化,将吹扫风向进行改变,由原来的风机抽取室外新风对陶瓷蓄热体进行正吹扫改为风机抽取RTO内部气体进行反向吹扫,将抽出来的烟气经风管引至RTO入口主风机之前,随着浓缩废气再次补入RTO内部,其优点为:
Therefore, the equipment manufacturer has optimized the blowing function by changing the blowing direction. Instead of using the original fan to extract outdoor fresh air for positive blowing of the ceramic heat storage body, the fan will extract the gas inside the RTO for reverse blowing. The extracted flue gas will be directed through the air duct to the front of the main fan at the RTO inlet, and as the concentrated exhaust gas is replenished into the RTO, its advantages are:
1)抽出的烟气随后又补入RTO内部,没有能量损失,节省了天然气等能源;2)吹扫风机抽出的烟气随后及时补入RTO,形成了一个内循环,不会造成RTO内部压力增加,且风平衡稳定。
1) The extracted flue gas is then fed into the RTO without energy loss, saving energy such as natural gas; 2) The flue gas extracted by the blowing fan is then promptly fed into the RTO, forming an internal circulation that does not cause an increase in internal pressure within the RTO, and the air balance is stable.